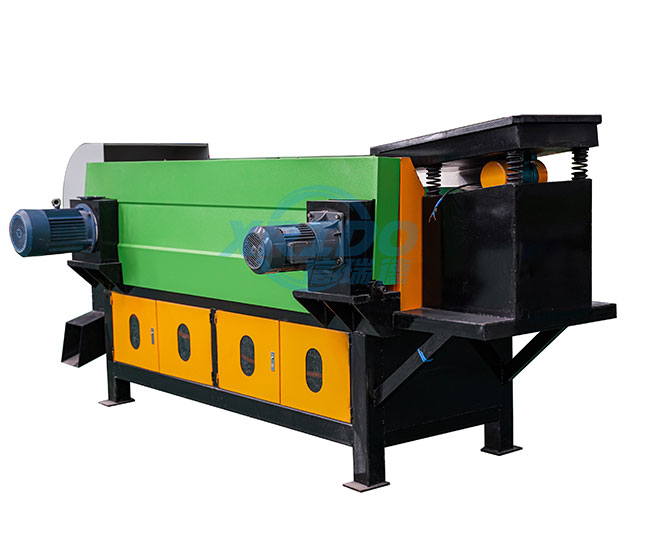
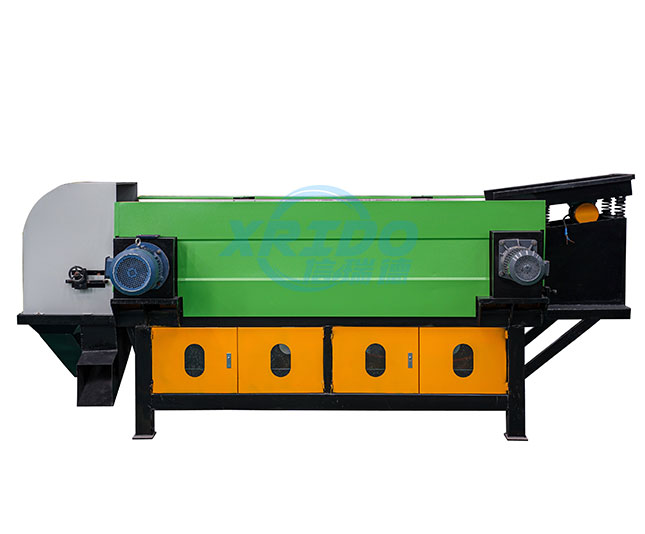
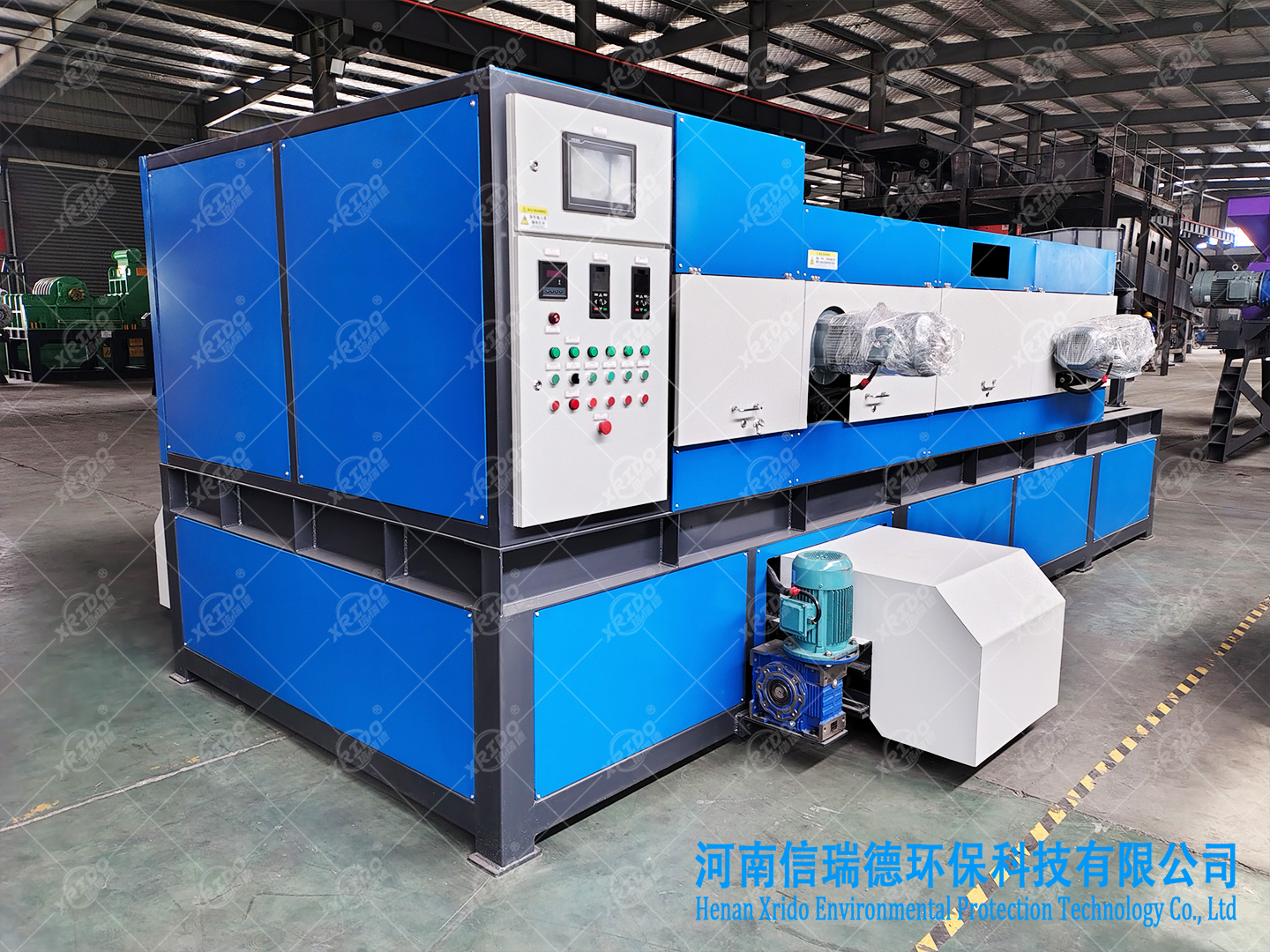
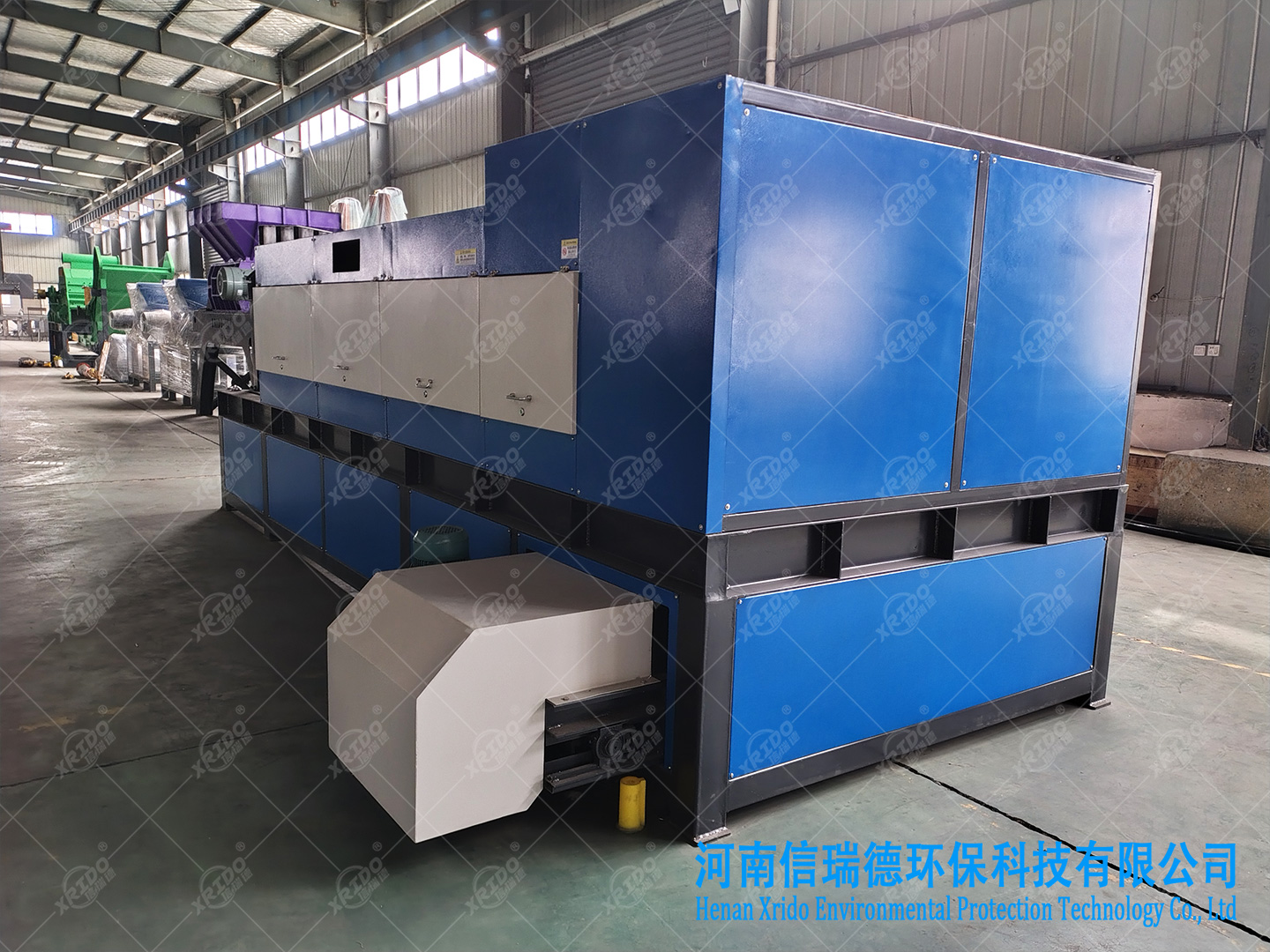
Eddy current separator
1.Effectively separate metals and increase recovery rates.
2.Compact overall size, flexible installation, high throughput.
3.Copper/aluminum separation purity >95% (impurity <5%), recovery rate >90%.Single machine processing capacity 5-30 tons/hour (depending on material density and particle size).
2025 Exhibition Information:
Time1:27(wed)-29(Fri) August 2025,
Location1 :KINTEX, Gyeonggi,KOREA,Exhibition location: Hall 10, D113.
Time2:November 10(Mon)-11(Tus), 2025
Location2 :Riyadh, Saudi Arabia,Recycling Expo Middle East 2025,C53.
Our E-mail: info@xrido.com
Whatsapp: +86-17513178882
Product Description
The Eddy Current Separator is used widely in the recycling industry to either recover or remove non-ferrous metals from non-metallic materials. Different designs enable the separation of small (down to 3mm) and large non-ferrous metals. The Eddy Current Separator (ECS) utilises magnetic forces to physically repel non-ferrous metals and enables separation from non-conductive materials. The eddy current separator is often supplied as part of a metal separation module with a first-stage drum magnet removing ferrous metals.
To maximise the separation and recovery of non-ferrous metals, Bunting has developed four different eddy current separator models:
High-Intensity Eccentric (HIE) ECS – for small non-ferrous metals down to 3mm;
High-Intensity Concentric (HIC) ECS – for small non-ferrous metals down to 10mm;
R Type ECS – for general recycling applications where non-ferrous metals are above 20mm;
Can Sorter (CS) ECS – A cost-efficient model designed specifically for the recovery of aluminium cans;
Eddy Current Separators commonly form part of a Metal Separation Module as a two-stage metal separator. Material initially passes over a Permanent Drum Magnet to remove and recover ferrous metals, leaving a non-magnetic fraction. The Eddy Current Separator then separates non-ferrous metals from the non-conductive remains.
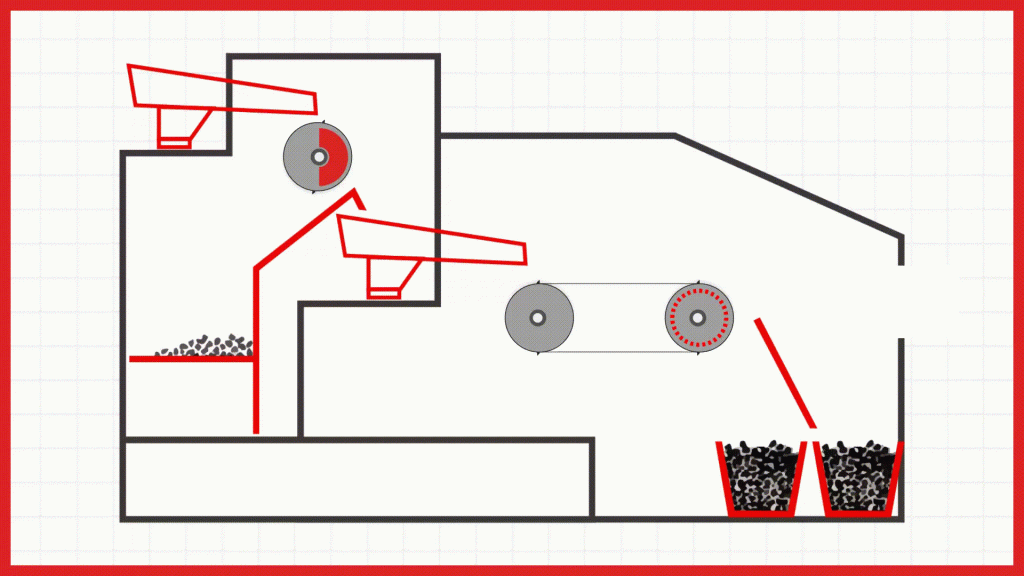
WORKING PRINCIPLE
1. An eddy current separator is a dual pulley conveyor system, where the non-metallic rotor cover houses an independently rotating high-speed magnetic rotor. Separation occurs when a non-ferrous metal particle (e.g. aluminium, copper or zinc) is conveyed into the magnetic zone. The non-ferrous metal particle is exposed to rapidly changing magnetic polarity. This induces ‘eddy currents’ into the particle generating an electrical current (Fleming’s left-hand rule) that subsequently creates its own magnetic field. The two magnetic fields oppose each other (i.e. North vs North pole repulsion), causing the repulsion of the non-ferrous metal particle and change in trajectory. The measured positioning of a splitter enables the separation of non-ferrous metals from non-metallic material due to the altered and unaltered material trajectories.
2. The speed of the magnetic rotor is dependent on the number of poles on the magnetic rotor and the application.
FEATURES
1. Effectively separates aluminum from the waste stream
2. Increases system recovery rates
3. Compact overall dimensions for installation versatility
4. High product throughput
Technical Parameters
Belt width(mm)
|
Effective Space(mm)
|
Separate Motor(kw)
|
Belt Driven Motor (KW)
|
Shaking Table Motor(kw)
|
Small Material (m3/h)
|
Big
Material (m3/h)
|
450
|
320
|
3
|
0.55
|
120
|
3
|
6
|
580
|
420
|
3
|
0.55
|
120
|
4
|
8
|
650
|
520
|
4
|
0.75
|
120
|
5
|
10
|
800
|
620
|
5.5
|
0.75
|
120
|
7
|
14
|
1000
|
820
|
5.5
|
1.1
|
2*120
|
9
|
18
|
1200
|
1050
|
7.5
|
1.1
|
2*120
|
11
|
22
|
1500
|
1350
|
7.5
|
1.1
|
2*120
|
14
|
28
|
Customer Photos